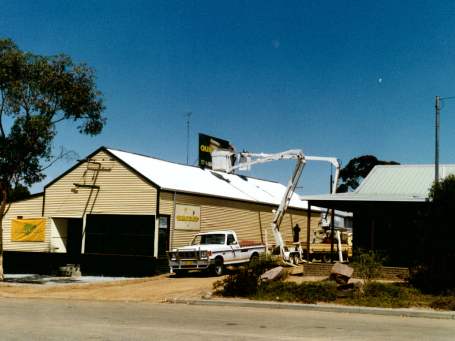
Our Processes
Making heavy-duty seat covers is a comprehensive process. Take a sneak peek behind the scenes, or should we say under the feathers, to see how it's done!
As an Australian owned and operated company, we value working with other Australian manufacturers wherever possible. We aim to use only Australian made materials, ensuring that each component in our seat covers is specifically designed to deal with harsh Australian conditions.
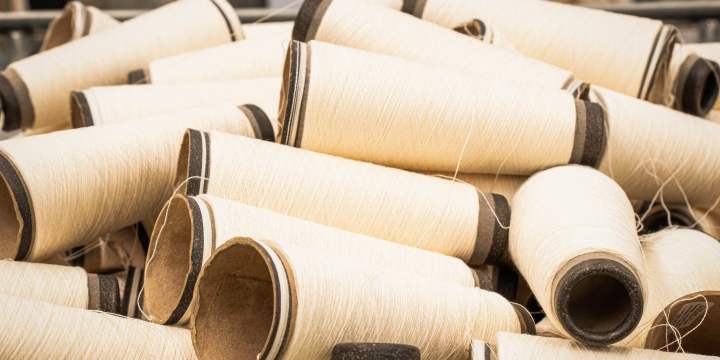
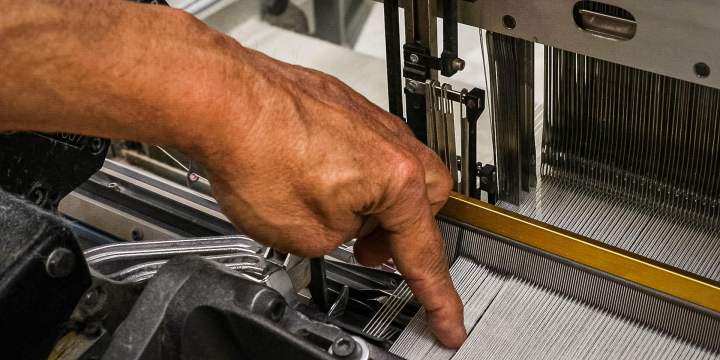
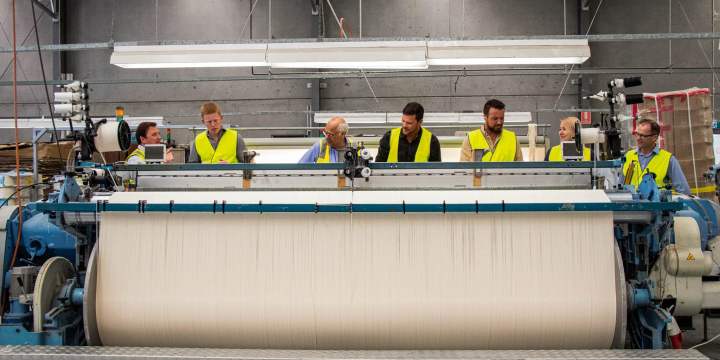
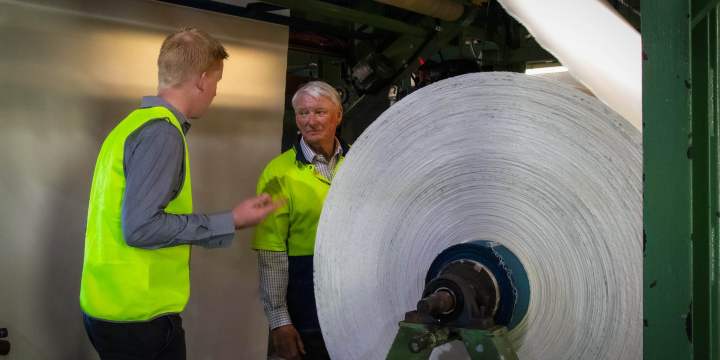
We specify that the materials we use must meet or exceed stringent Australian Standards for quality and durability. Our suppliers test every batch of materials as part of their production process and once received by Black Duck is further inspected for compliance. Only materials meeting our specifications are used in our production processes.
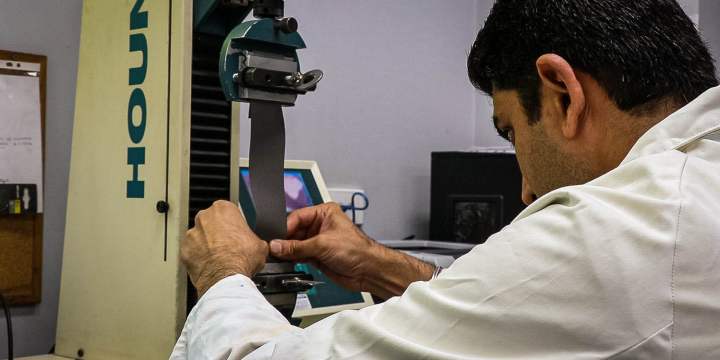
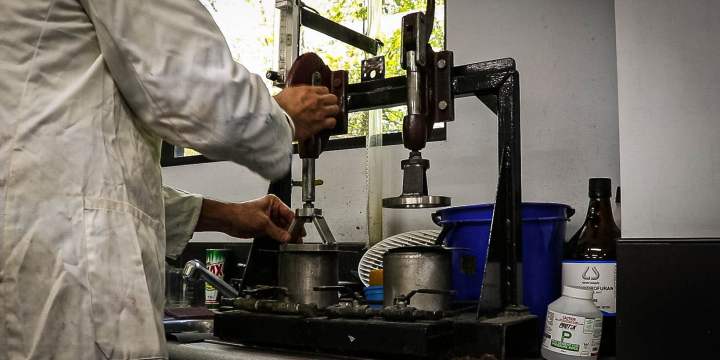
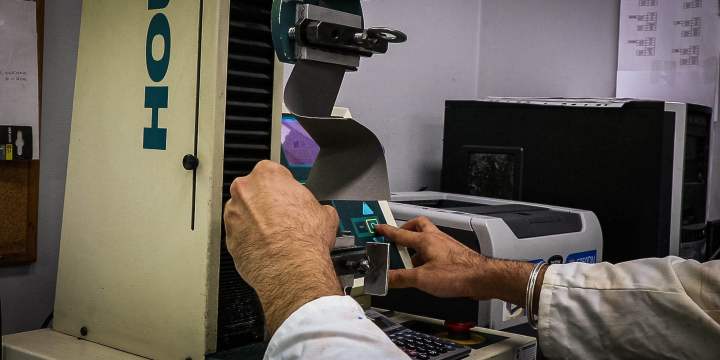
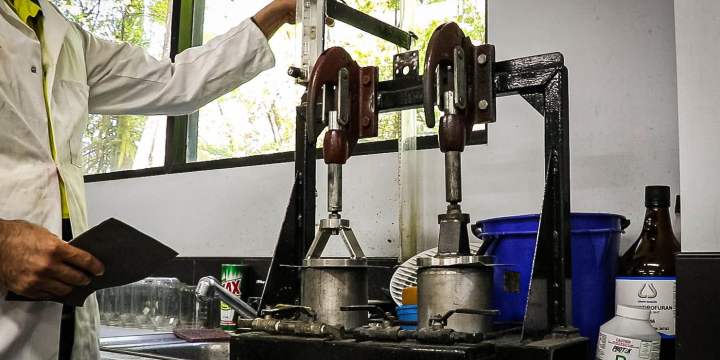
Black Duck SeatCovers take into consideration several factors when deciding which vehicles we make seat covers for. As we specialize in heavy-duty seat covers for vehicles that experience substantial wear and tear, such as 4WD's, utes, vans, trucks, agricultural equipment and other industrial vehicles, patterns for these are developed as soon as the vehicles become available to our Product Development Team.
For other vehicles, we keep a log of enquiries that come through, and once a vehicle has generated enough interest we will develop patterns to suit and notify everyone who has registered their interest.
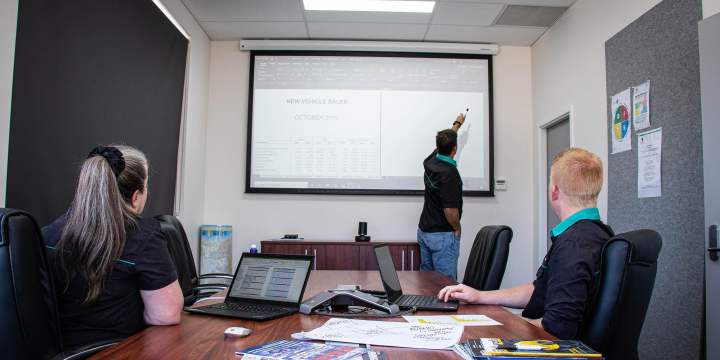
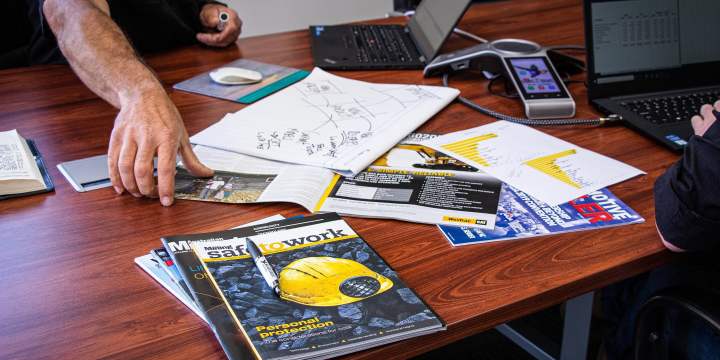
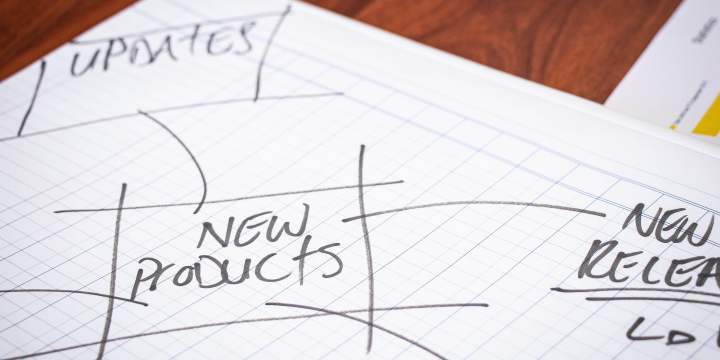
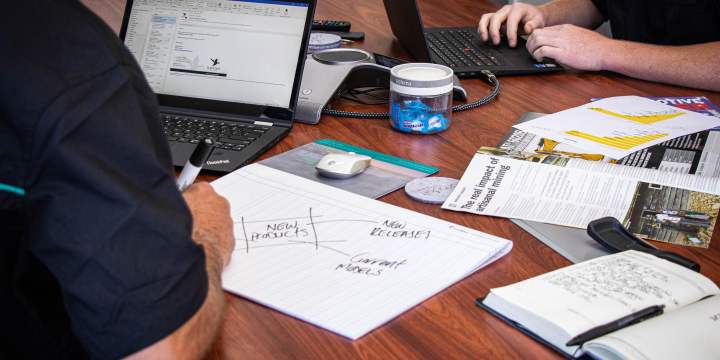
Our experienced pattern makers go through a comprehensive process to create tailored-fit seat covers that are designed specifically for each seat - no "universal-fit" or "one size fits all" here!
If you see our Black Duck SeatCovers van out around in Perth, it is likely heading to work on a new pattern. The van is equipped with everything required to create a pattern from start to finish and allows us to make multiple revisions of a pattern to achieve that perfect fit.
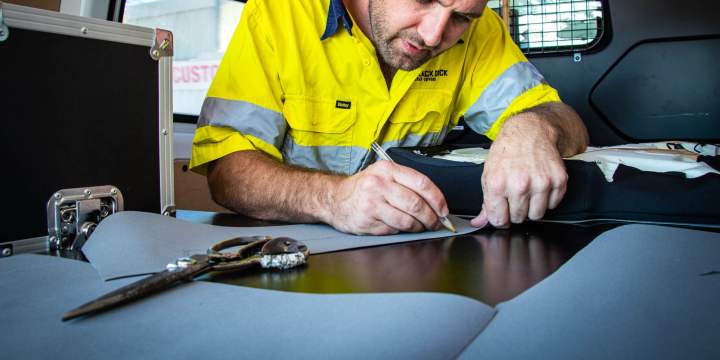
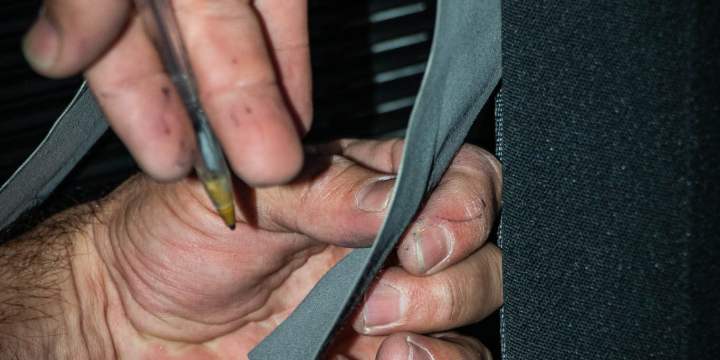
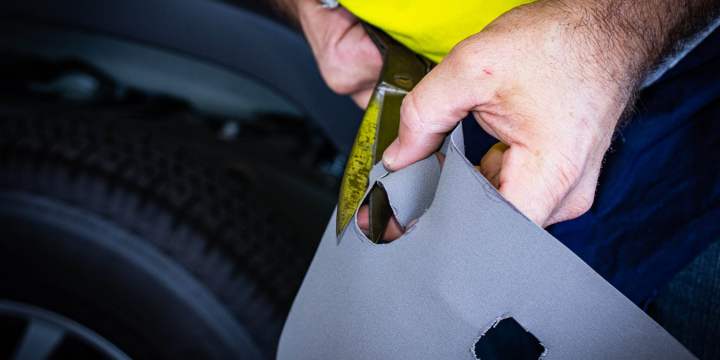
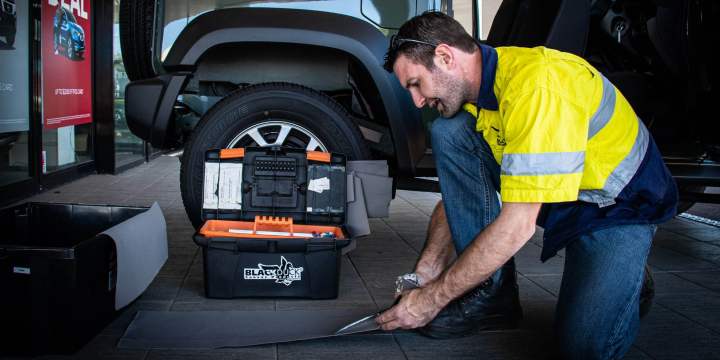
Once a pattern has been finalised and gone through a fitting process, it gets digitized and cut files are created for consistency and accuracy in the preparation phase. The Product Development Team then produce guidelines for how to assemble each seat cover, these guidelines are referred to as "top sheets". These files are then compiled with "pick sheets" that outline every single component that goes into making a complete seat cover. Once this has been done, the pattern is ready for production.
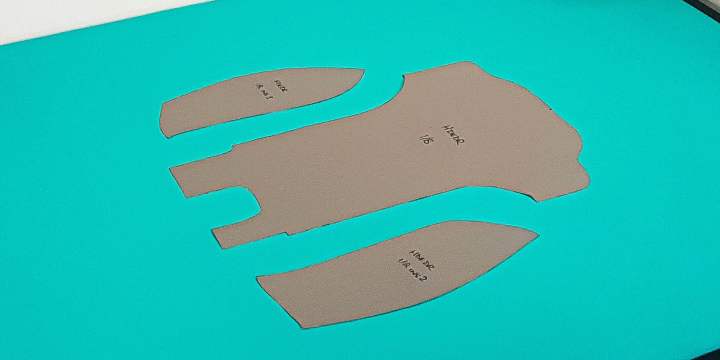
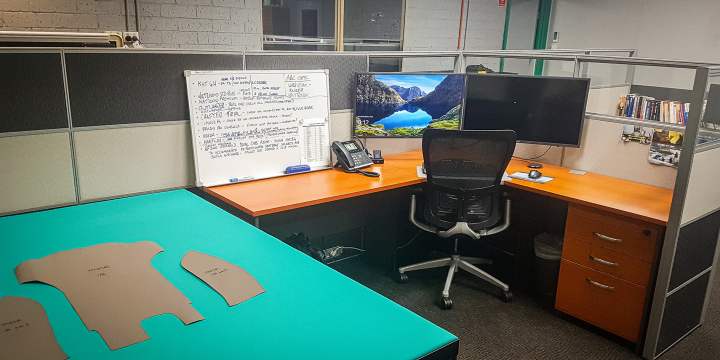
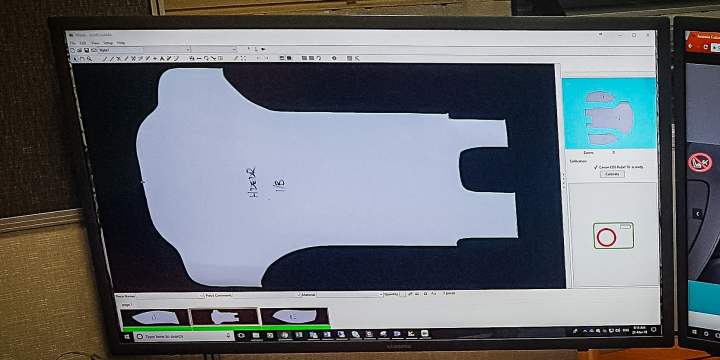
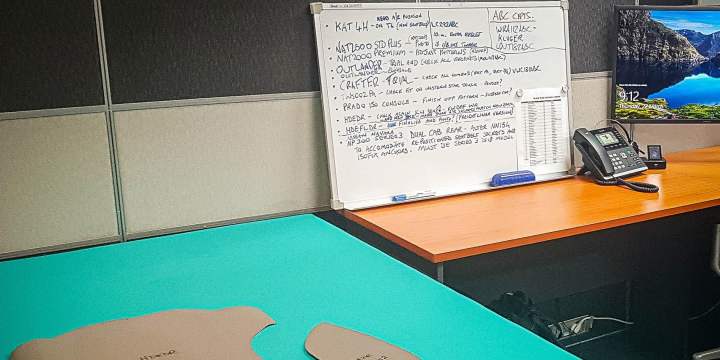
When a customer orders a seat cover for their vehicle, a work order is created in our system. This starts a process that begins with our cutting team accessing the digitized cut file and putting this through one of our CNC cutting machines. These machines can precision cut up to 20 layers of material at a time and each pattern can have up to 40 individual components.
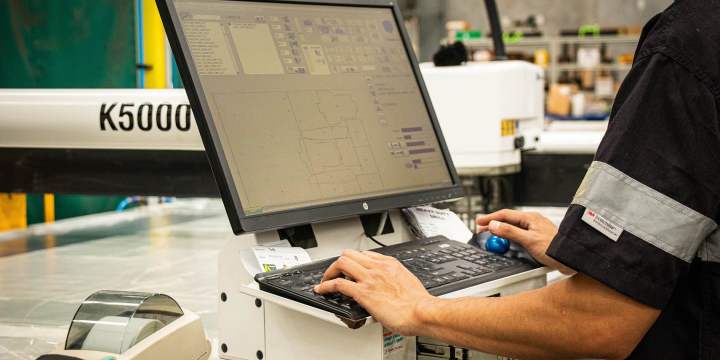
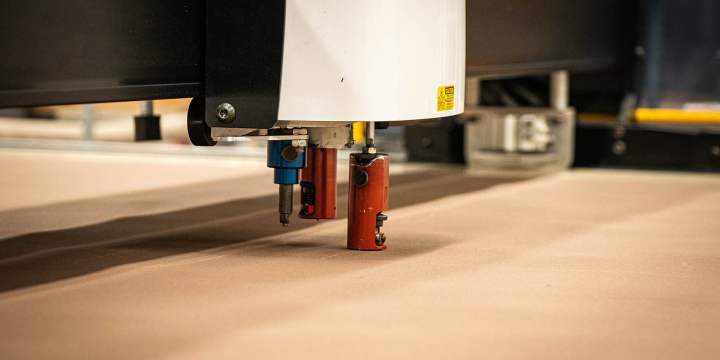
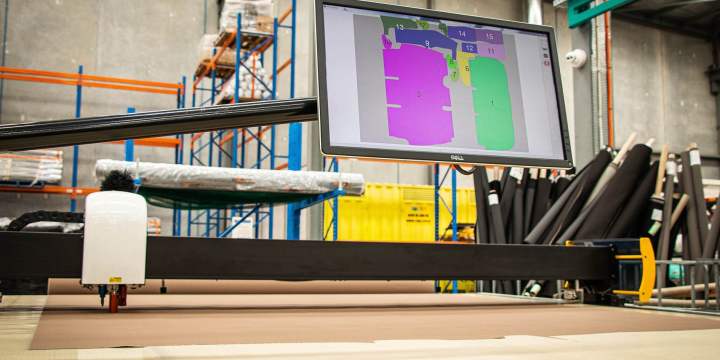
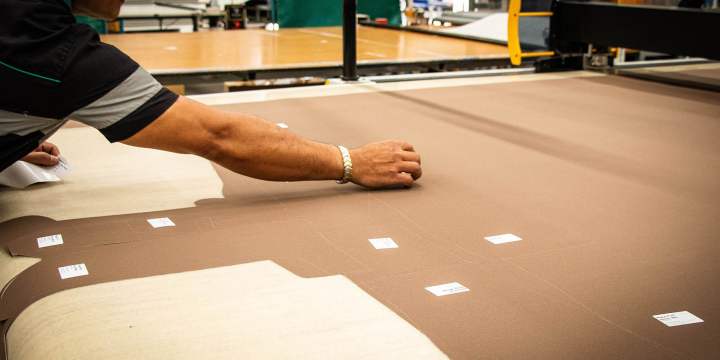
The Black Duck® logo has built a reputation for quality and durability over the last 40 years. The logo takes pride of place on the backrest of the seat cover so that you know you are buying genuine Black Duck SeatCovers backed by a quality promise you can trust.
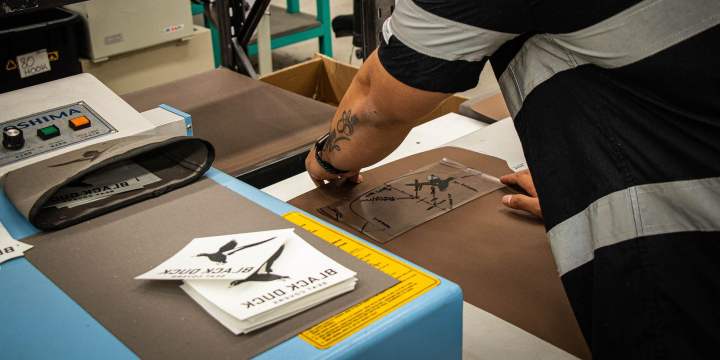
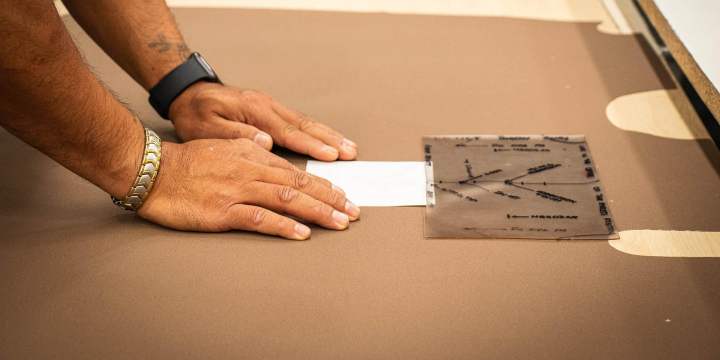
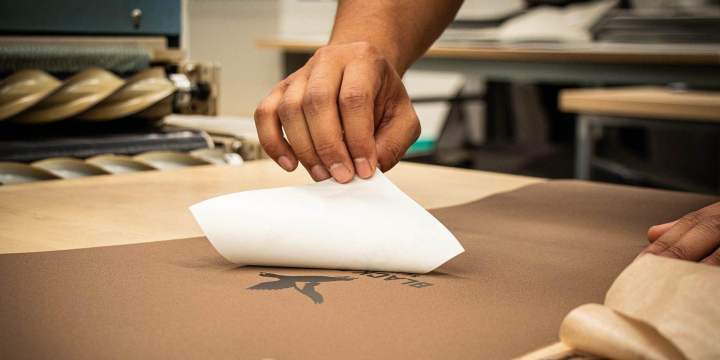
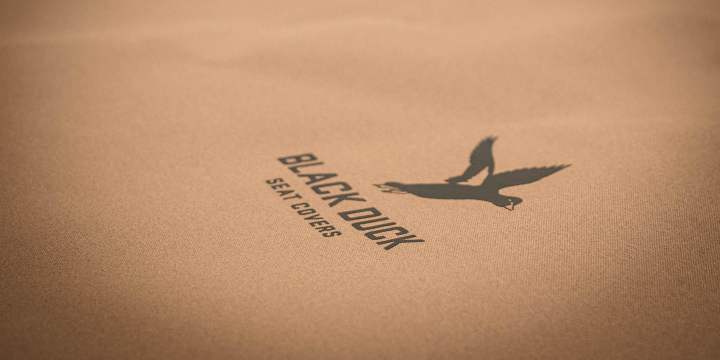
The completed cuts get handed over to our layup team, who are responsible for preparing the materials ready for sewing. The layup team accesses a library of "top sheets", which consist of sewing instructions and a component list that make up the seat cover.
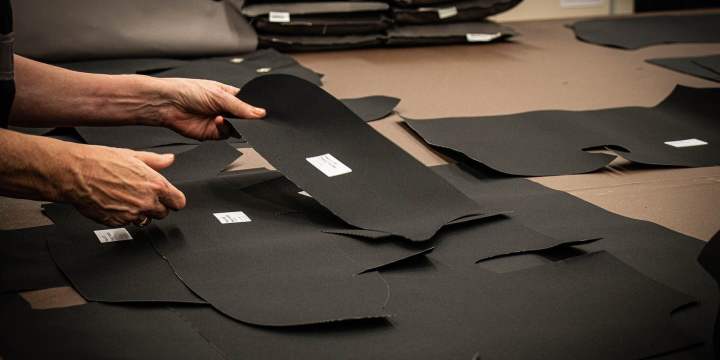
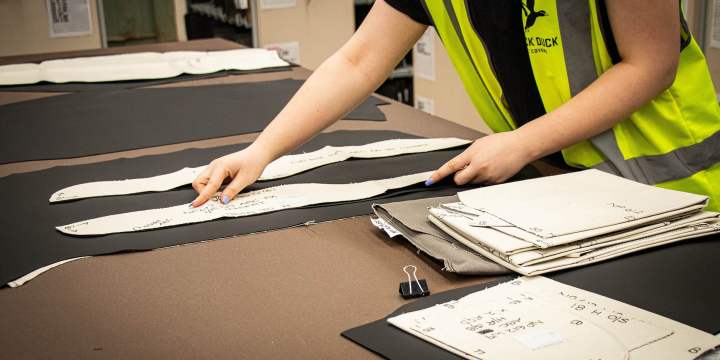
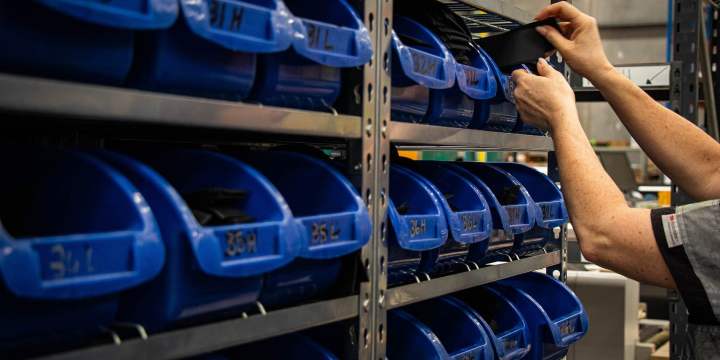
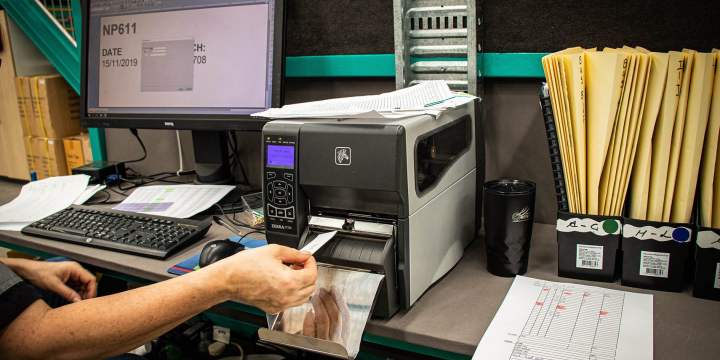
Our highly skilled team of sewing machinists, who collectively have over 250 years of experience between them, then get to work crafting the seat covers. Due to the intricacy of our patterns, we have a diverse skills matrix we can draw on to ensure that each task is allocated to the most suited machinist.
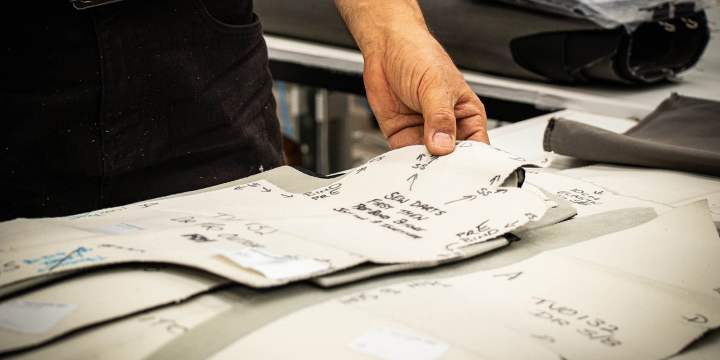
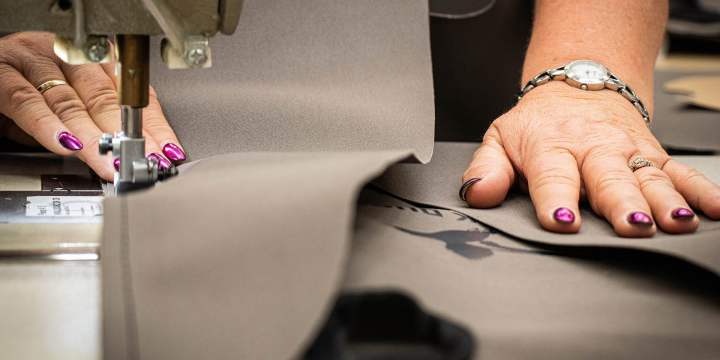
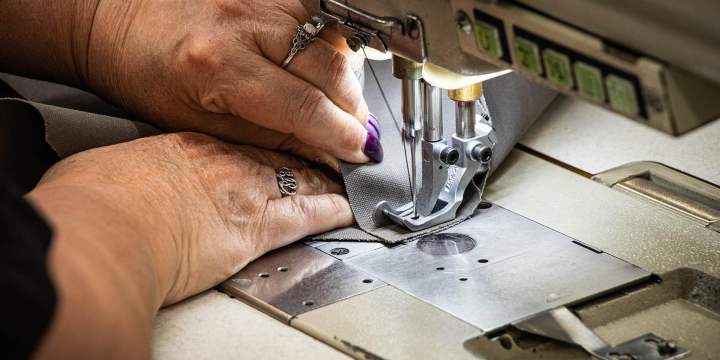
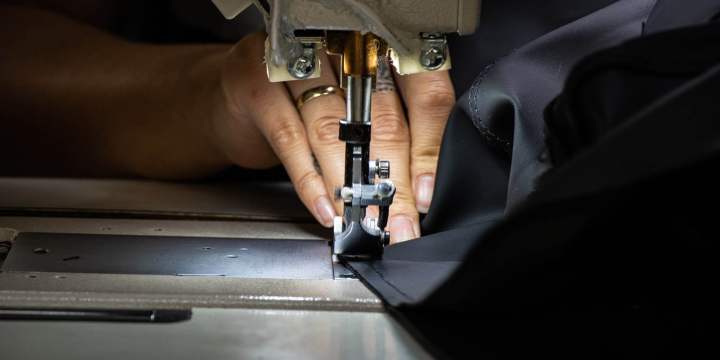
If your vehicle has seat fitted air-bags, your seat cover will feature an air-bag compatible seam. This seam is sewn on a special machine, using special thread designed to ensure the air-bag can still deploy in the event of an accident. We conduct independent testing of our air-bag compatible seat covers to ensure that our products adhere to ADR.
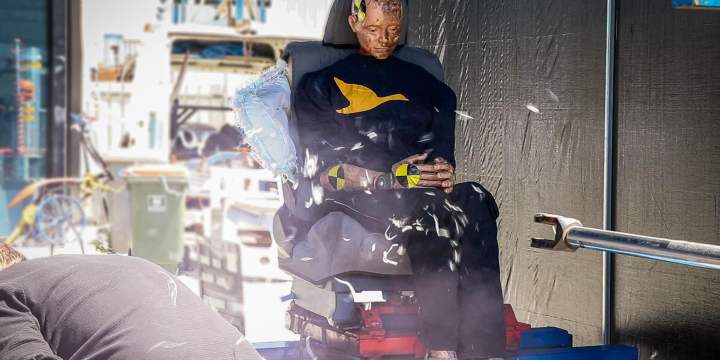
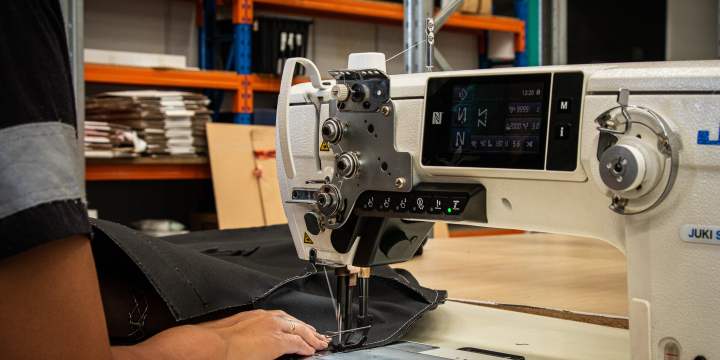
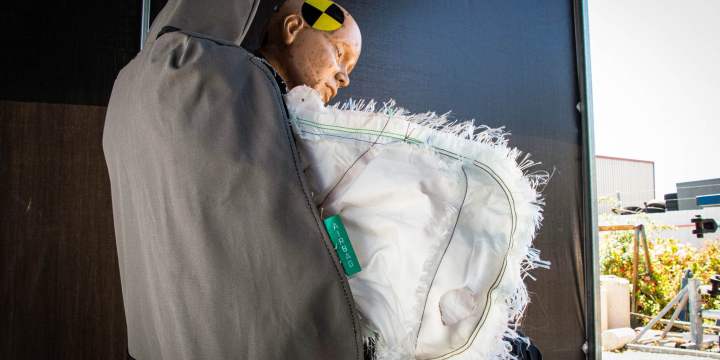
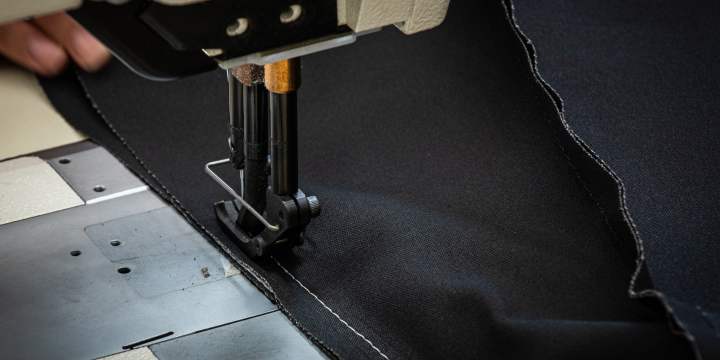
Taking a completed seat cover and executing the finishing touches such as sealing the edges with a herringbone trim adds a protective edging to the seat cover and finished off the modern look.
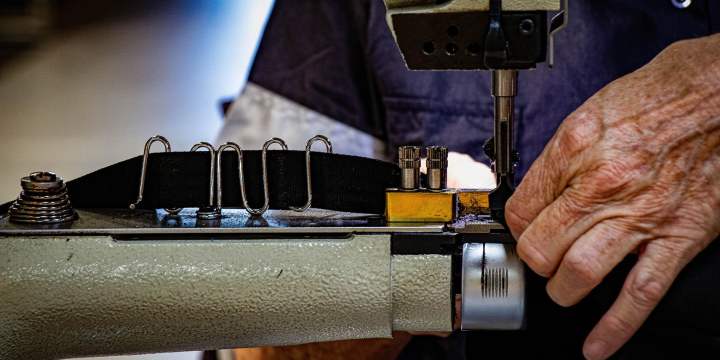
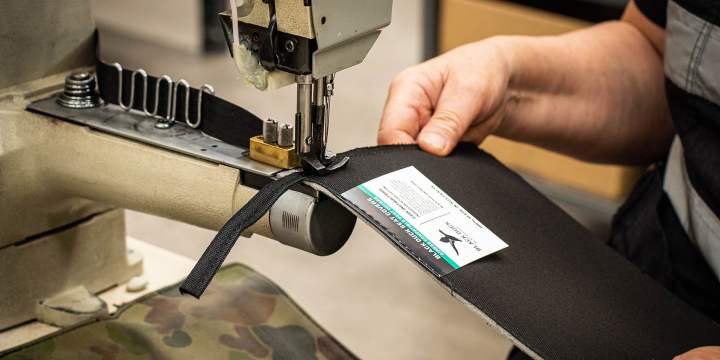
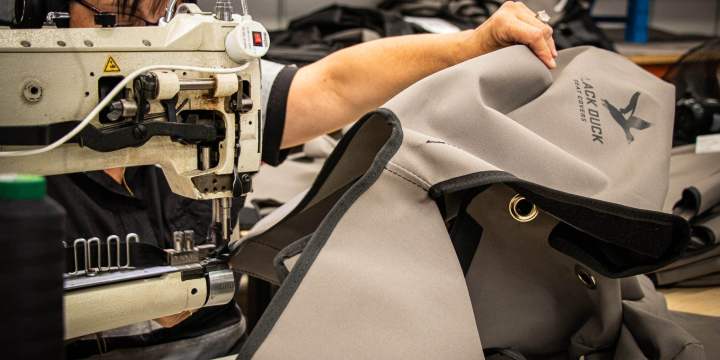
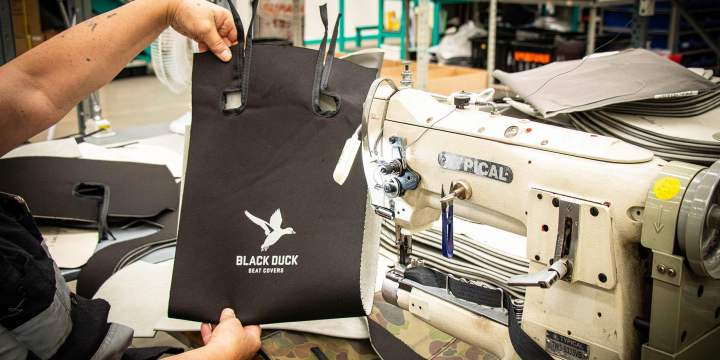
Each person involved in the production process takes responsibility for the quality production of our products. We also have a team of experienced supervisors who check at each stage of the production process to ensure consistency and that internal quality standards are met.
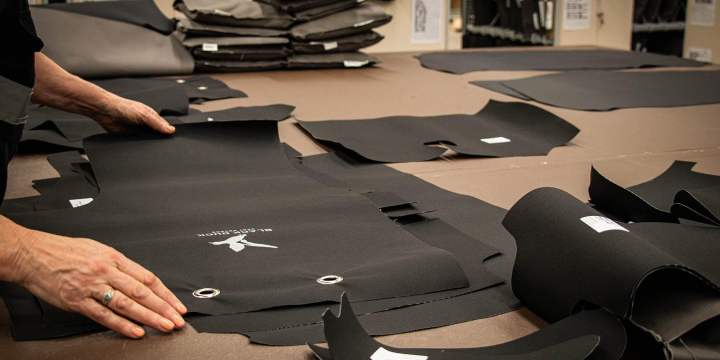
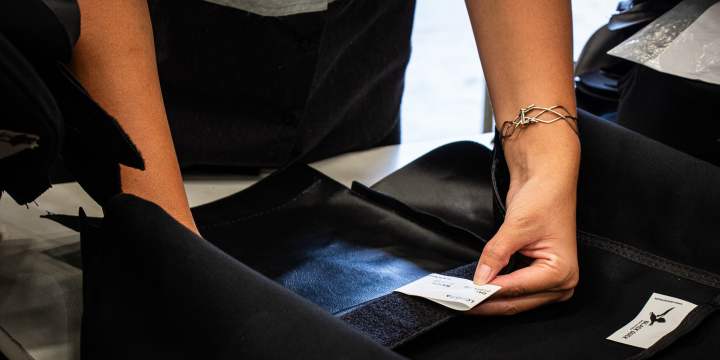
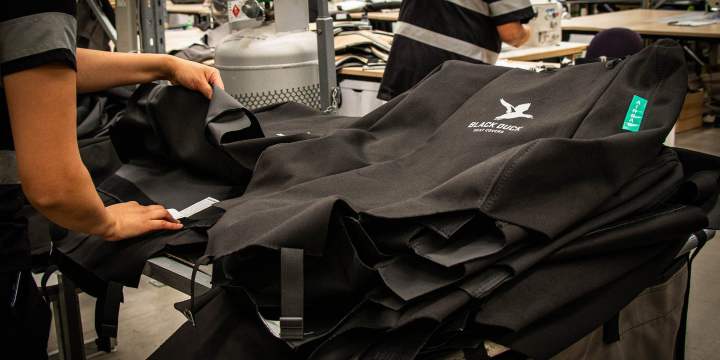
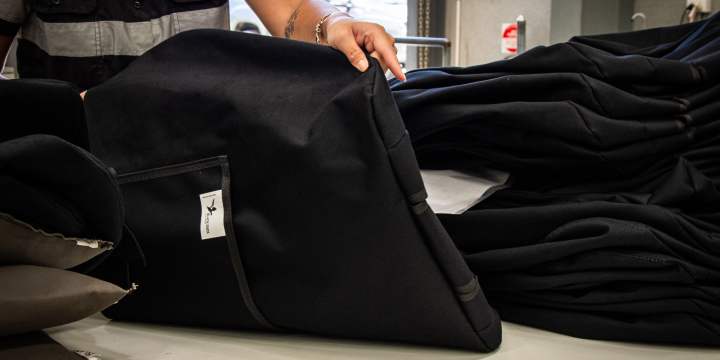
All of our products are individually packaged by hand, not by machines. Depending on the seat configuration, the seat cover components are laid out on a flat surface and then combined into one neat package. It is then folded based on achieving the most effective utilization of space.
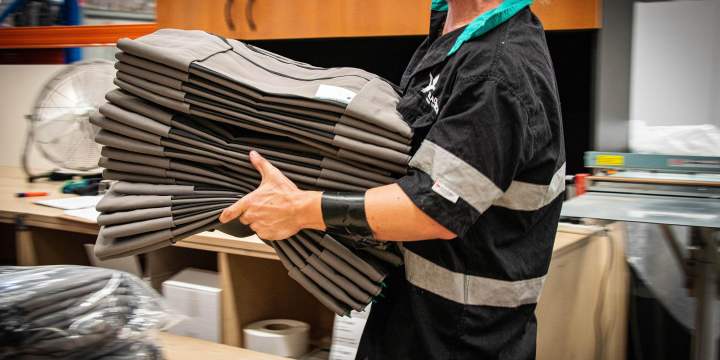
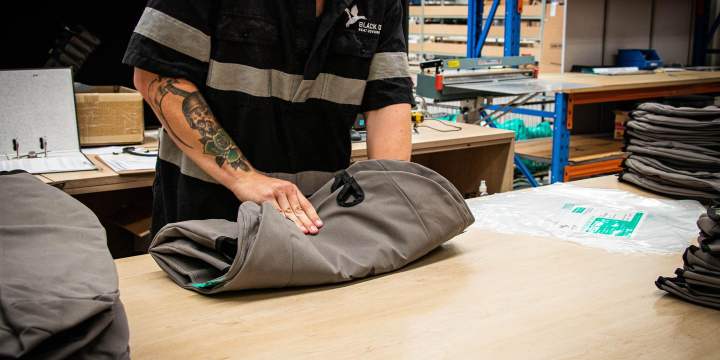
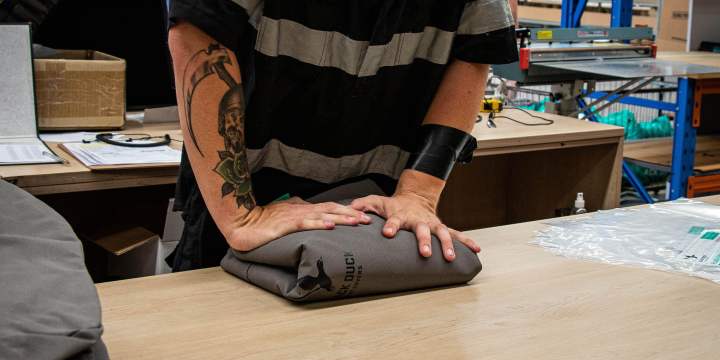
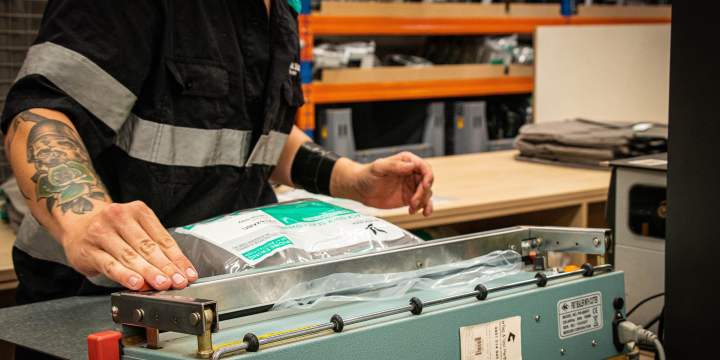
We are really proud of the fact that we have over 3000 seat cover cut files. We try to keep our more popular products in stock at our WA manufacturing facilities, however, if your seat covers are not in stock, or you have chosen 1 of 12 material and colour combinations it may take up to 1-2 weeks from the date of order for your covers to be ready for dispatch. Once your seat covers are ready, we use a network of reliable freight partners to ensure you get your order as quickly and securely as possible.
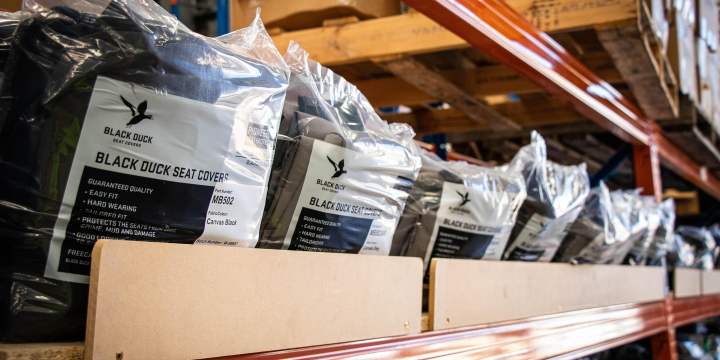
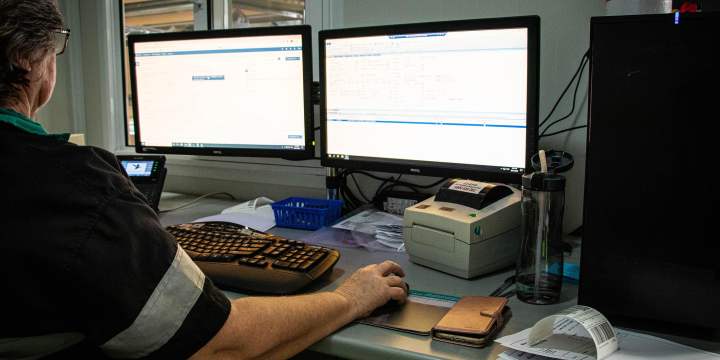
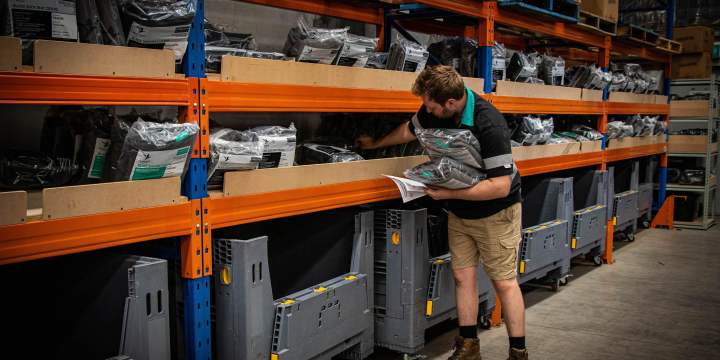
